To develop a comprehensive supply chain playbook tailored to the needs of an emerging market for a global FMCG electronics brand. The focus was improving supply chain efficiency, reducing costs, and enhancing responsiveness to market demands. This case study outlines the approaches and key methodologies to achieve these objectives.
Background
The project was undertaken for a mobile manufacturing facility with a turnover of $300 million (2000 Crore INR). The facility faced several challenges typical of emerging markets, including:
- High logistics and transportation costs
- Long cycle times and delays
- Inefficient inventory management
- Poor coordination between supply chain partners
- Regulatory and compliance hurdles
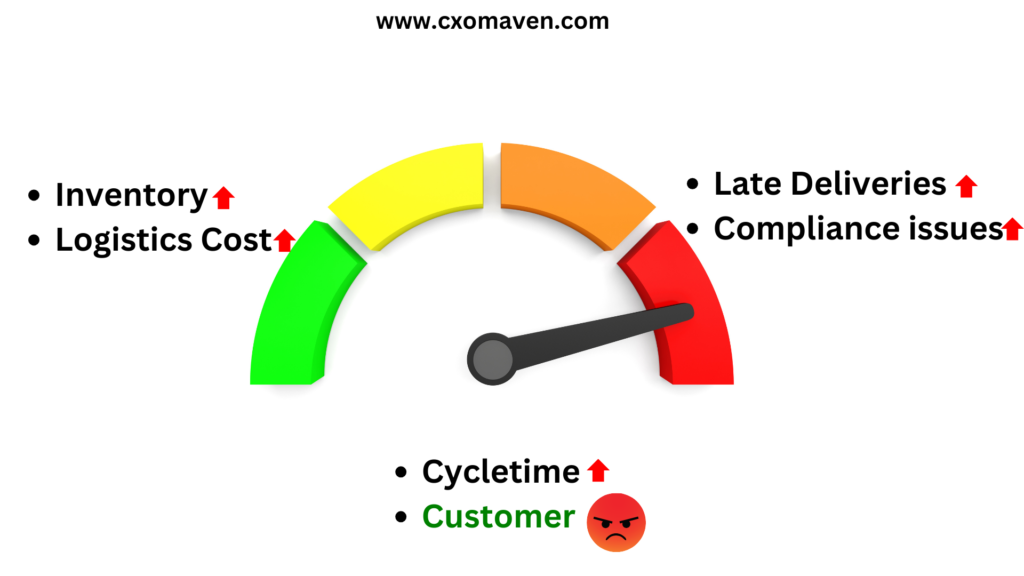
Methodology
The supply chain playbook project followed the Lean Six Sigma DMAIC (Define, Measure, Analyze, Improve, Control) methodology to address these challenges systematically.
Define Phase
The project team identified key problem areas:
- High logistics and transportation costs
- Long cycle times and delays
- Inefficient inventory management
Management’s focus was on reducing the overall supply chain cost, improving cycle times, and enhancing coordination between supply chain partners.
Measure Phase
The team conducted an in-depth analysis of the current supply chain processes, assessing various parameters such as:
- Transportation costs
- Cycle time from order receipt to delivery
- Inventory levels and turnover rates
- Supplier performance and compliance
The baseline performance was established based on historical data and benchmarking against industry standards.
Analyze Phase
The analysis phase involved identifying the root causes of inefficiencies through:
- Cause-and-effect diagrams
- 5 Why analysis
- Value Stream Mapping (VSM)
Key issues identified included:
- Non-optimized transportation routes and carrier choices
- Delays in customs clearance and regulatory compliance
- High inventory levels due to poor demand forecasting and planning
- Lack of real-time visibility into supply chain processes

Improve Phase
Several improvement initiatives were implemented to optimize the supply chain:
- Value Stream Mapping (VSM): Mapping the current state and designing a future state with streamlined processes.
- Mode Conversion: Shifting a higher percentage of shipments from air to sea to reduce costs.
- Carrier Optimization: Selecting carriers with better transit times and lower costs.
- Inventory Management: Implementing Just-in-Time (JIT) inventory systems to reduce excess inventory and improve turnover rates.
- Technology Integration: Leveraging advanced analytics and real-time tracking systems to enhance visibility and coordination.
- Supplier Collaboration: Establishing closer relationships with suppliers to improve compliance and performance.
Specific actions taken included:
- Redesigning transportation routes to minimize delays and costs
- Implementing a standardized process for customs clearance and regulatory compliance
- Introducing real-time tracking systems for better visibility into the supply chain
- Conducting regular supplier audits and performance reviews
Control Phase
To sustain the improvements, the team introduced:
- Daily monitoring of key supply chain performance metrics
- Regular training programs on Lean Six Sigma and supply chain best practices
- Continuous improvement initiatives through regular reviews and audits
- Implementation of control charts to track key performance indicators (KPIs)
Outcomes
The implementation of the supply chain playbook led to significant improvements:
- Cost Reduction: Overall transportation and logistics costs were reduced by 15%.
- Cycle Time Reduction: Total cycle time from order receipt to delivery was reduced by 20%.
- Inventory Turnover Improvement: Inventory turnover rates improved by 30%, leading to reduced holding costs.
- Enhanced Visibility: Real-time tracking systems provided better visibility into supply chain processes, leading to improved decision-making.
- Supplier Performance: Supplier compliance and performance improved, resulting in fewer delays and better quality.
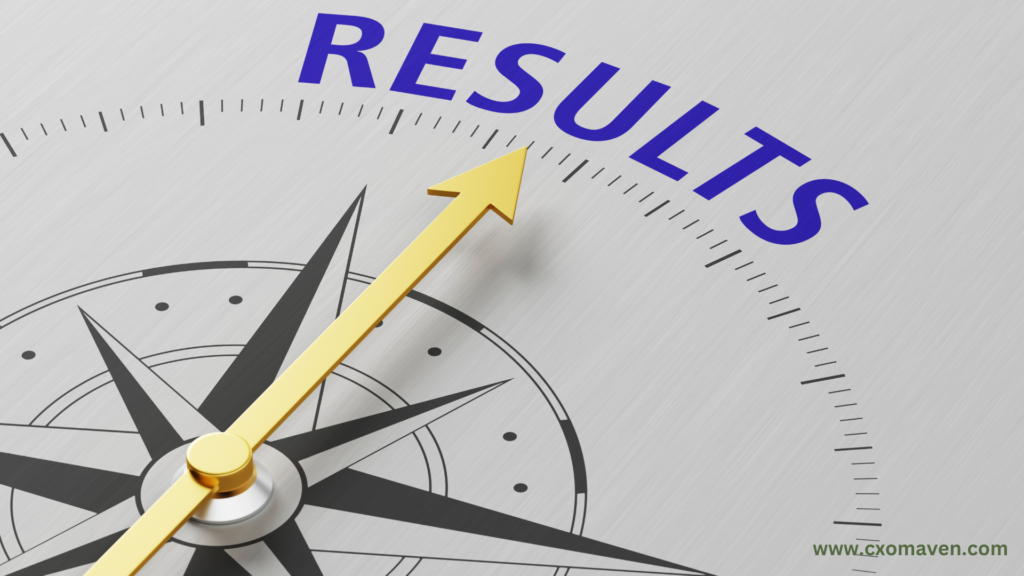
Conclusion
This case study demonstrates the effectiveness of a well-structured supply chain playbook in optimizing supply chain processes for a global FMCG electronics brand. By addressing key issues such as high logistics costs, long cycle times, and inefficient inventory management, the project significantly improved operational efficiency, reduced costs, and enhanced overall supply chain responsiveness.
Acknowledgments
The successful implementation of this project was due to the collective efforts of the dedicated project team, which included representatives from the logistics, procurement, quality, and finance departments.
Future Plans
Building on the success of this project, the organization plans to further optimize its supply chain by:
- Expanding the use of Value Stream Mapping to other regions and processes
- Continuously reviewing and improving transportation routes and carrier choices
- Enhancing collaboration with suppliers and logistics partners for better efficiency and cost savings
By continuously focusing on supply chain optimization, the facility aims to maintain its competitive edge in the global FMCG electronics market and drive further growth and success.