Introduce and implement a Should-Cost analysis as the primary costing methodology for all direct categories to achieve significant cost savings and improve supplier collaboration for a healthcare company. The focus was on critical components such as PCBAs, power supplies, fabricated components, machining parts, cables, harnesses, and plastics categories. This case study outlines the timeline, approaches, and outcomes of the Should Cost implementation.
Background
In June 2006, the healthcare company initiated a project to develop templates for various procurement categories, aiming to gain better cost insights and drive negotiations. The project spanned multiple phases, each targeting specific goals to optimize procurement costs and enhance supplier relationships.
Methodology
The project followed a structured approach, beginning with identifying parts and forming a dedicated team, followed by supplier engagement, cost analysis, and negotiation.
June
Initiation: Templates were developed for PCBs, power supplies, fabricated components, machining parts, cables, harnesses, and plastics categories. These templates provided a standardized framework for cost analysis.
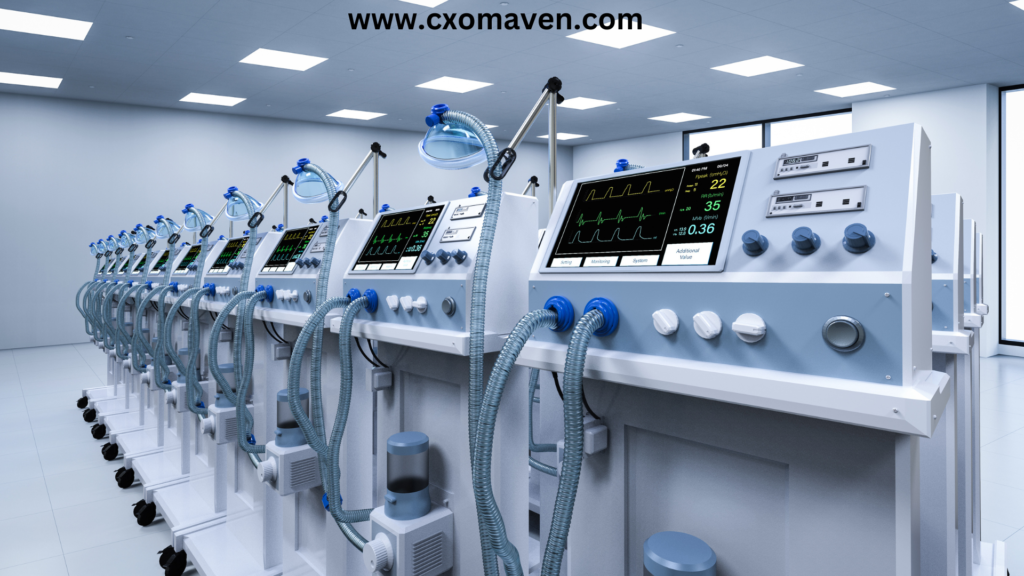
September
Parts Identification: A total of 267 parts were identified for the Should Cost analysis. These parts were categorized based on their impact on cost and procurement complexity.
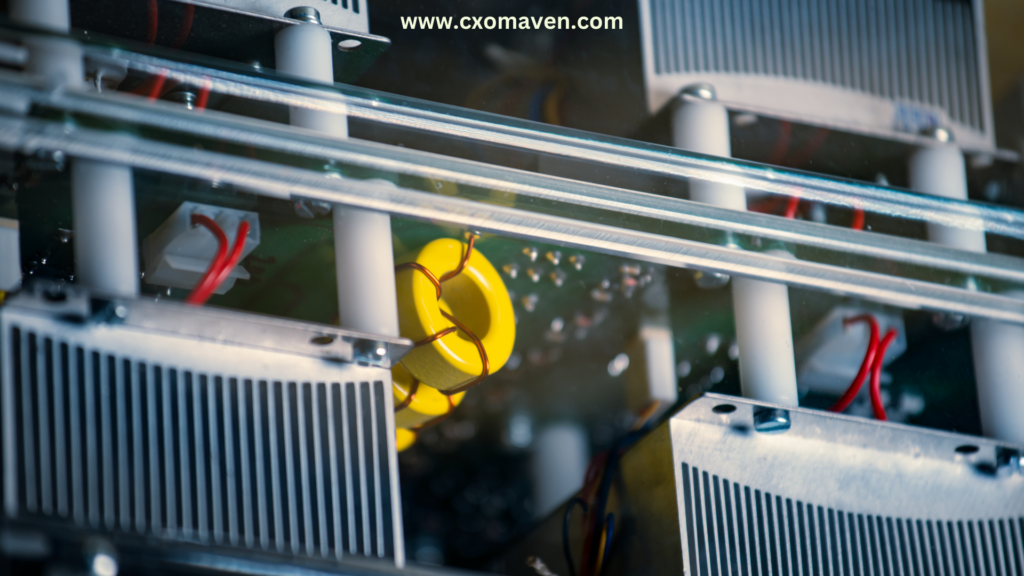
November
Team Formation: A dedicated team consisting of Sourcing Leaders (SL) and Supplier Quality Experts (SQE) was formed to drive the project.
- Selection of A-Class Parts: The team focused on 117 high-impact (A-Class) parts for detailed cost analysis.
- Supplier Selection: Strategic suppliers from procurement categories were selected for collaboration.
- Stakeholder Buy-In: The team secured buy-in from key supplier stakeholders, ensuring their commitment to the project.
- Supplier Visits: The team conducted visits to supplier facilities to gather detailed cost data and understand production processes.
- Cycle Time Action Workouts (AWOs): Action Workouts were conducted to streamline cycle times and identify cost-saving opportunities.
- Should Cost Analysis: Detailed Should Cost analysis was performed for the identified parts to establish benchmark costs.
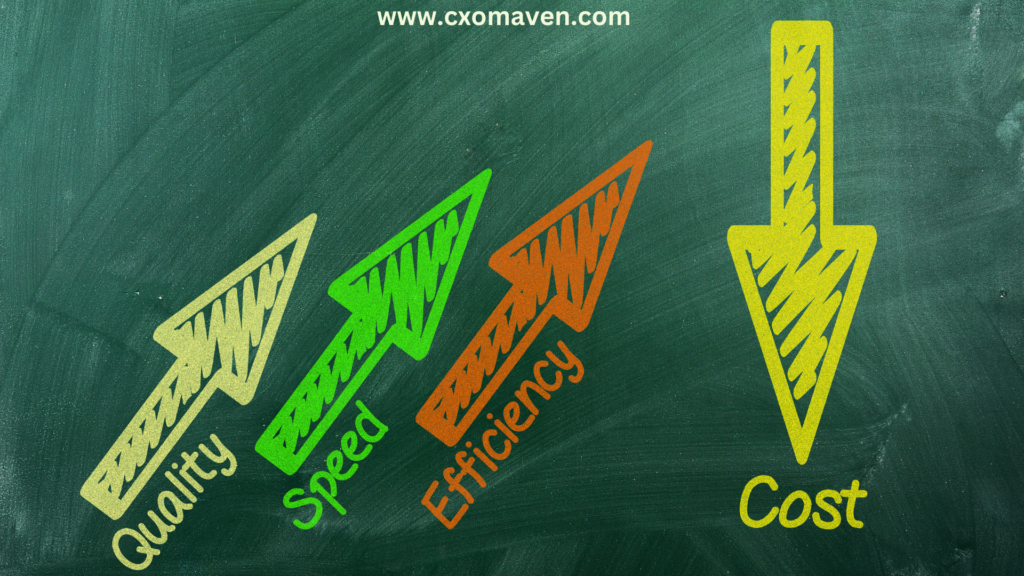
December
- Negotiations: Based on the Should Cost analysis, the team entered negotiations with suppliers, achieving significant cost reductions.
- Annual Savings: The negotiations resulted in $1.4 million in annual savings.
- Cost Avoidance: Additional cost avoidance of $0.45 million was achieved for 137 parts, further enhancing cost efficiency.
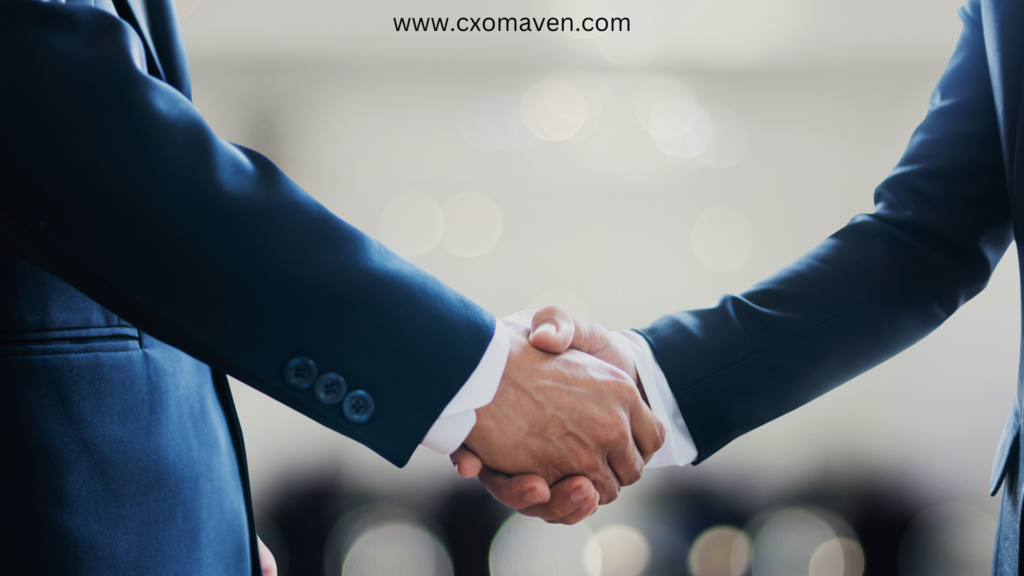
June of next year Onwards
- Continuous Improvement: The team continued to work on packaging and label templates, and developed an in-circuit tester template to further streamline procurement processes.
- Ongoing AWOs: Cycle time reduction Action Workouts were conducted regularly to sustain the cost savings and improve process efficiency.
Outcomes
The implementation of Should Cost analysis led to significant improvements:
- Cost Savings: The project achieved a total of $1.85 million in cost savings and avoidance, exceeding initial expectations.
- Improved Supplier Collaboration: Enhanced relationships with strategic suppliers led to better negotiation outcomes and ongoing process improvements.
- Standardization: The development of standardized templates for cost analysis improved the accuracy and efficiency of procurement processes.
- Cycle Time Reduction: Regular Action Workouts helped in reducing cycle times, leading to faster procurement and production cycles.
Conclusion
This case study demonstrates the effectiveness of Should Cost analysis in driving cost savings and improving supplier collaboration for a healthcare company. By focusing on high-impact parts and engaging strategic suppliers, the project significantly enhanced procurement efficiency and achieved substantial financial benefits.
Acknowledgements
The successful implementation of this project was due to the collective efforts of the dedicated project team, including Sourcing Leaders, Supplier Quality Experts, and key supplier stakeholders.
Future Plans
Building on the success of this project, the organization plans to expand the Should Cost analysis to other procurement categories and regions. Continuous improvement initiatives, including regular Action Workouts and supplier engagements, will be maintained to ensure sustained cost efficiency and operational excellence.