The project objective is to enhance the efficiency of a startup mobile manufacturing facility by implementing Lean Manufacturing principles. The goal was to address high work-in-progress (WIP), reduce customer complaints, and streamline material flow on the shop floor. This case study outlines the steps taken to achieve these results and make this facility a world-class manufacturing site.
Background
The mobile manufacturing facility, with a turnover of $300 million (2000 Crore INR), faced several challenges typical of a startup phase, including:
- High WIP inventory
- Poor visual controls
- Parts mix-up leading to customer dissatisfaction
- Excess inventory and materials scattered on the shop floor
- Lack of proper storage and organization
- Absence of standardized processes such as kitting and 5S (Sort, Set in order, Shine, Standardize, Sustain)
Methodology
The project followed the Lean Six Sigma DMAIC (Define, Measure, Analyze, Improve, Control) methodology to systematically address the issues.
Define Phase
The project team identified key problem areas:
- High WIP inventory
- Poor visual factory controls
- Frequent parts mix-up
Management concerns were centered around improving the cash conversion cycle and addressing customer complaints.
Measure Phase
The team conducted an operations review meeting to assess the condition of the shop floor. Key observations included:
- Material is scattered and there are no visual controls
- Excess inventory and no proper racks for storage
- Lack of operator skills and material availability
- No streamlined material flow and poor line balance
A decision matrix was used to prioritize these issues based on their impact on stakeholders, including customers, employees, quality, business, and finance teams.
Analyze Phase
Brainstorming sessions and cause-and-effect diagrams helped identify the root causes of high WIP, such as:
- Improper material replenishment and disorganized workflow
- Lack of visual controls and line imbalance
- No accountability and poor training
A 5 Why analysis further drilled down into specific issues like uncontrolled buffers and line imbalances.

Improve Phase
The team implemented several Lean tools and methodologies to address the identified issues:
- Value stream mapping and SMED (Single-Minute Exchange of Die)
- Introduction of single-piece flow and Just-in-Time (JIT) production
- Batch size reduction and 3C (Clear, Clean, Check) 5S concepts
- Total Productive Maintenance (TPM) and streamlined layout
The implementation included a Kanban system to improve the cash conversion cycle, reduce inventory, and create a continuous flow. This involved:
- Standardization of bins and kitting processes
- Establishment of supermarket concepts and FIFO (First In, First Out) visibility
- Line balancing to reduce manpower and improve ergonomics
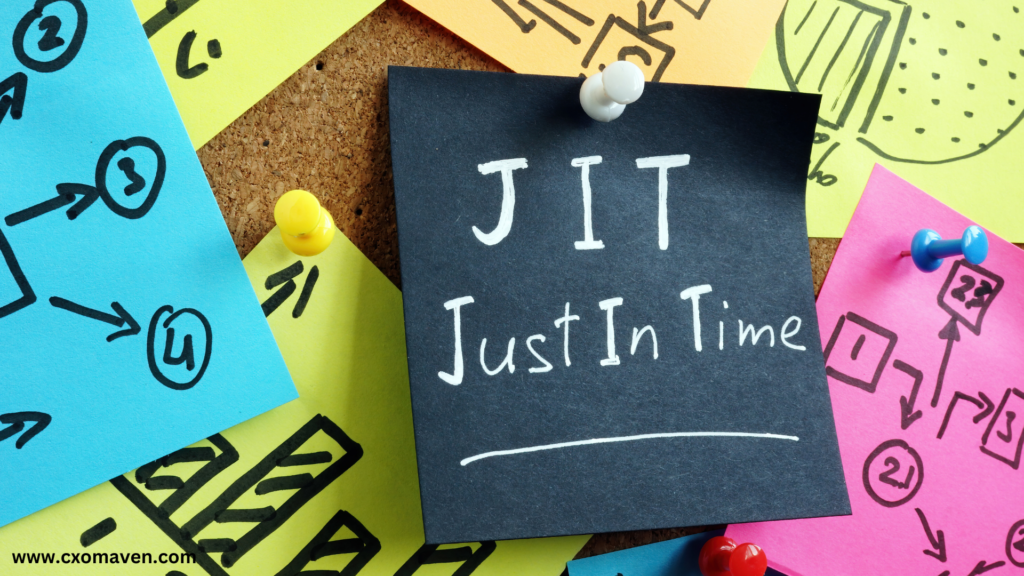
Control Phase
To sustain the improvements, the team introduced:
- Daily tracking of WIP status
- Training and awareness programs on Kanban and Lean principles
- Visual management and audit scorecards for 3C 5S concepts
- Regular reviews and continuous monitoring through Lean tracker systems
Outcomes
The implementation of Lean Manufacturing principles led to significant improvements:
- WIP inventory reduced from an average of 5.3 days to less than 1 day
- Customer complaints decreased due to better parts management and visual controls
- Floor space saving of 377 square meters, resulting in a cost saving of $703K
- Material movement distance reduced, leading to an annual cost saving of $198K
- Overall financial benefits amounted to $957K annually
The project received appreciation from senior leadership and was recognized as a benchmark for other facilities within the organization.

Conclusion
This case study demonstrates the effectiveness of Lean Manufacturing principles in transforming a startup mobile manufacturing facility. By addressing key issues such as high WIP, poor visual controls, and parts mix-up, the project significantly improved operational efficiency, reduced costs, and enhanced customer satisfaction. The systematic approach using Lean Six Sigma DMAIC and Lean tools ensured sustained improvements and established a foundation for continuous growth and excellence.
Acknowledgments
The successful implementation of this project was due to the collective efforts of the dedicated project team, which included representatives from planning, lean coordination, manufacturing, production, process engineering, industrial engineering, quality, and warehouse management.
Future Plans
Building on the success of this project, the organization planed to horizontally deploy Kanban in backend assembly lines and network assembly lines.
Additionally, further efforts were to be made to reduce end-to-end cycle time through value stream mapping by the fourth quarter of the following year.